The Evolution of 3D Printing: From Concept to Industry Standard
The journey of 3D printing from a niche technology to an integral part of modern manufacturing has been nothing short of revolutionary. Initially, it was primarily used as a tool for rapid prototyping in academic and research settings. However, advancements in materials science, software algorithms, and hardware capabilities have propelled 3D printing into mainstream industries like automotive, aerospace, healthcare, and consumer electronics. This transformation is largely due to the increasing affordability and accessibility of 3D printers, which has democratized access for small businesses and hobbyists alike.
The early stages of 3D printing were marked by limited material options and constrained print sizes. However, as technology progressed, materials such as thermoplastics, metals, ceramics, and even biocompatible substances became viable. This diversification not only broadened the design possibilities but also opened up new applications in complex industries like aerospace, where lightweight components are crucial for fuel efficiency. Furthermore, advancements in precision have allowed for intricate internal structures that were previously unattainable through traditional manufacturing methods.
Today, 3D printing is no longer just a tool for rapid prototyping; it has become an integral part of the production cycle. Companies can now produce parts directly from digital models with minimal setup time and cost. This shift has significantly reduced lead times and enabled on-demand manufacturing, which is particularly beneficial in industries where customization and quick turnaround are paramount.
3D Printing’s Impact on Prototyping
In the realm of product development, 3D printing stands out as a game-changer for prototyping. Traditional methods often involved lengthy processes such as tooling or molding, which were not only time-consuming but also prohibitively expensive for early-stage designs. The advent of 3D printing has drastically reduced these barriers, allowing designers and engineers to iterate quickly on their ideas.
One of the most significant advantages of 3D printing in prototyping is its ability to produce highly detailed parts with complex geometries. This capability allows designers to experiment with form factors that would otherwise be difficult or impossible to achieve using conventional methods. For example, intricate internal structures can be printed to simulate the performance and functionality of a final product without needing full-scale assembly. This enables engineers to validate design concepts early in the development cycle, leading to more efficient problem-solving and fewer costly mistakes.
Moreover, 3D printing has introduced an unprecedented level of customization into prototyping processes. With the ability to print unique or specialized components, teams can tailor prototypes to specific user needs and preferences, thereby enhancing usability testing and market research efforts. This level of adaptability is particularly valuable in industries like automotive and consumer electronics where design iterations are frequent and customer feedback plays a crucial role.
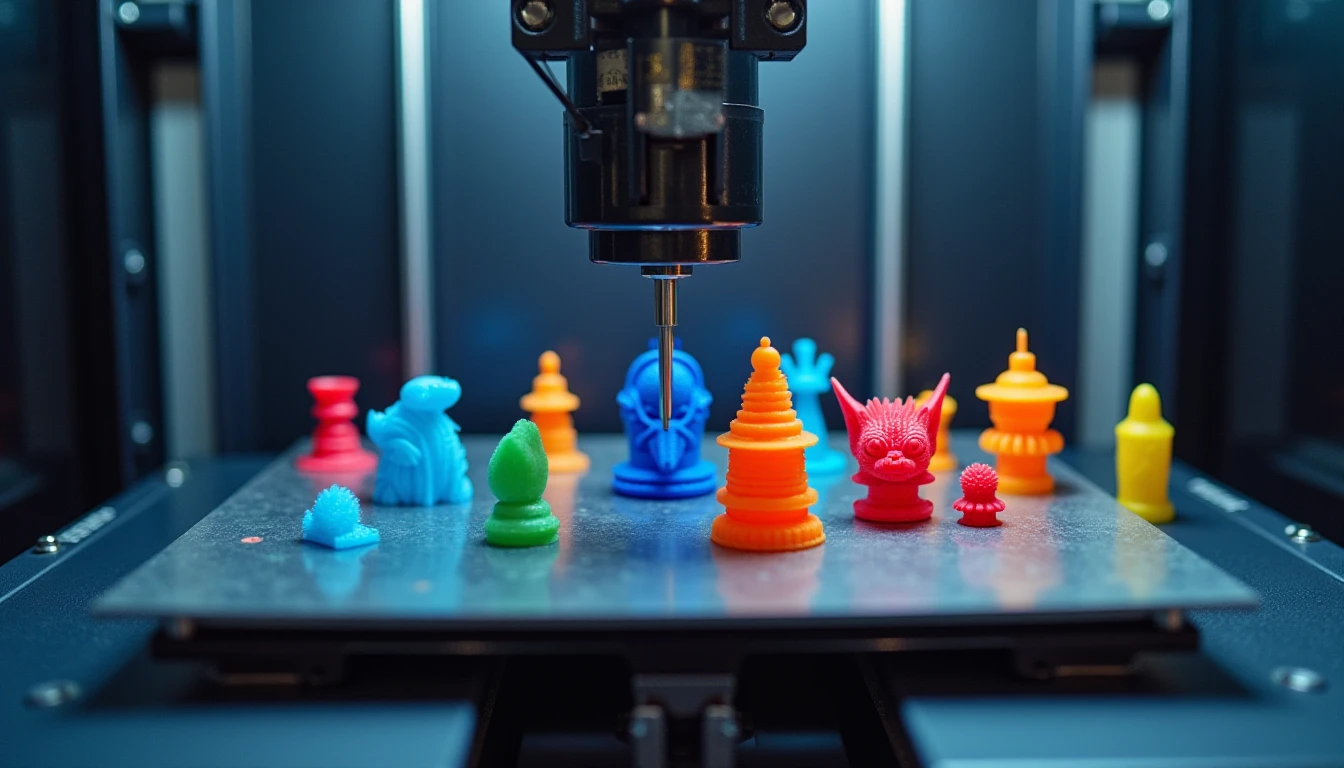
Manufacturing Applications: Efficiency and Innovation
The integration of 3D printing into manufacturing processes has unlocked new levels of efficiency and innovation across various industries. By allowing for the production of parts directly from digital models, companies can bypass traditional manufacturing steps like tooling, machining, or casting. This not only reduces lead times but also minimizes material waste by producing parts with precise dimensions.
One of the most compelling benefits of 3D printing in manufacturing is its potential for on-demand production. Instead of maintaining large inventories of spare parts, companies can print them as needed, reducing warehousing costs and improving supply chain agility. This approach is particularly advantageous in industries where specific components are used infrequently but require quick replacement to avoid costly downtime.
Furthermore, 3D printing enables manufacturers to integrate complex internal structures into their designs without additional assembly steps. For instance, aerospace companies can print lightweight yet structurally sound parts that enhance fuel efficiency and reduce emissions. Similarly, medical device manufacturers benefit from the ability to produce intricate implants and surgical tools tailored to individual patient needs. This level of customization not only improves product performance but also streamlines manufacturing processes by eliminating the need for multiple components or assembly steps.
Material Science: The Backbone of 3D Printing
The success of 3D printing in both prototyping and manufacturing is deeply intertwined with advancements in material science. As the technology has matured, so too have the range and quality of materials available for use in 3D printing. From thermoplastics to metals, ceramics, and even biocompatible substances, the variety of printable materials reflects a broad spectrum of applications.
Thermoplastics remain one of the most widely used materials due to their versatility, ease of processing, and relatively low cost. Materials like PLA (polylactic acid) and ABS (acrylonitrile butadiene styrene) are commonly employed in prototyping and functional parts. These plastics offer good mechanical properties while being easy to print with, making them ideal for applications ranging from consumer products to automotive components.
Metals have also emerged as a critical material category for 3D printing, particularly in industries where high performance is paramount. Metal alloys such as titanium, aluminum, and stainless steel are used extensively in aerospace, medical devices, and industrial machinery. The ability to print metal parts with complex internal structures allows manufacturers to produce lightweight yet strong components that would be difficult or impossible to achieve through traditional methods. This has significant implications for reducing material costs and improving product performance.
In the healthcare sector, biocompatible materials have opened up new possibilities in 3D printing. Materials such as titanium alloys and PEEK (polyether ether ketone) are used to create implants that can be seamlessly integrated into the human body. These materials not only provide structural support but also facilitate faster healing times due to their compatibility with biological tissues.
Sustainability: A New Frontier for 3D Printing
As environmental concerns become increasingly prominent, many industries are turning to 3D printing as a more sustainable alternative to traditional manufacturing methods. The technology’s ability to reduce material waste and energy consumption makes it an attractive option for companies looking to lower their carbon footprint.
One of the most significant ways 3D printing contributes to sustainability is through reduced material usage. Traditional subtractive manufacturing processes often result in substantial amounts of scrap material, which must then be disposed of or recycled. In contrast, additive manufacturing techniques like 3D printing build parts layer by layer from digital models, minimizing waste and optimizing material use. This approach not only reduces raw material consumption but also lowers the energy required for production.
Moreover, 3D printing enables localized production, reducing reliance on long supply chains that contribute to higher transportation emissions. By producing components closer to their point of use, companies can decrease their carbon footprint while improving delivery times and responsiveness to market demands. This shift towards decentralized manufacturing aligns well with broader sustainability goals, particularly in industries where customization or rapid prototyping are essential.
In addition to material efficiency, 3D printing offers opportunities for recycling and reuse. Many 3D printers can now accept recycled plastics as feedstock, further reducing the demand for virgin materials. As these technologies continue to evolve, they will play an increasingly important role in creating circular economies where waste is minimized and resources are reused.
Challenges and Future Directions
Despite its many advantages, 3D printing faces several challenges that must be addressed before it can achieve its full potential across various industries. One of the primary concerns is scalability. While 3D printers have made significant strides in producing high-quality parts at smaller scales, scaling up to produce large batches or complex assemblies remains a challenge.
Another issue lies in standardization and certification. As more companies adopt 3D printing for production, there will be increasing demand for consistent quality assurance across different machines and materials. Without standardized protocols and certifications, it may become difficult to ensure that parts printed by one machine meet the same specifications as those produced by another. This is especially critical in industries like aerospace or medical devices where safety and reliability are paramount.
Looking ahead, the future of 3D printing holds exciting possibilities. Advances in multi-material printing will allow for the creation of products with integrated functionalities, such as electronics embedded directly into structures. Additionally, breakthroughs in nanotechnology could lead to materials that possess unique properties like superconductivity or self-healing capabilities. These innovations promise to push the boundaries of what can be achieved through 3D printing and further integrate it into mainstream manufacturing processes.
As these challenges are overcome and new technologies emerge, 3D printing will continue to evolve from a specialized tool to an indispensable part of modern production systems. Its ability to accelerate innovation while promoting sustainability positions it as a key player in shaping the future of manufacturing and beyond.